What will the manufacturing of tomorrow look like? Industrial details are becoming smaller; products get to the market with less waste, faster, and on time. Even the most manual processes are turning towards automation. Innovations in machine learning, industrial computer vision, and robotics are revolutionizing the production lines and supply chains.
In particular, artificial intelligence (AI) and computer vision hold great potential for tackling real-life problems, from ophthalmology diagnosis with retinal images to processing millions or even billions of documents for content analysis.
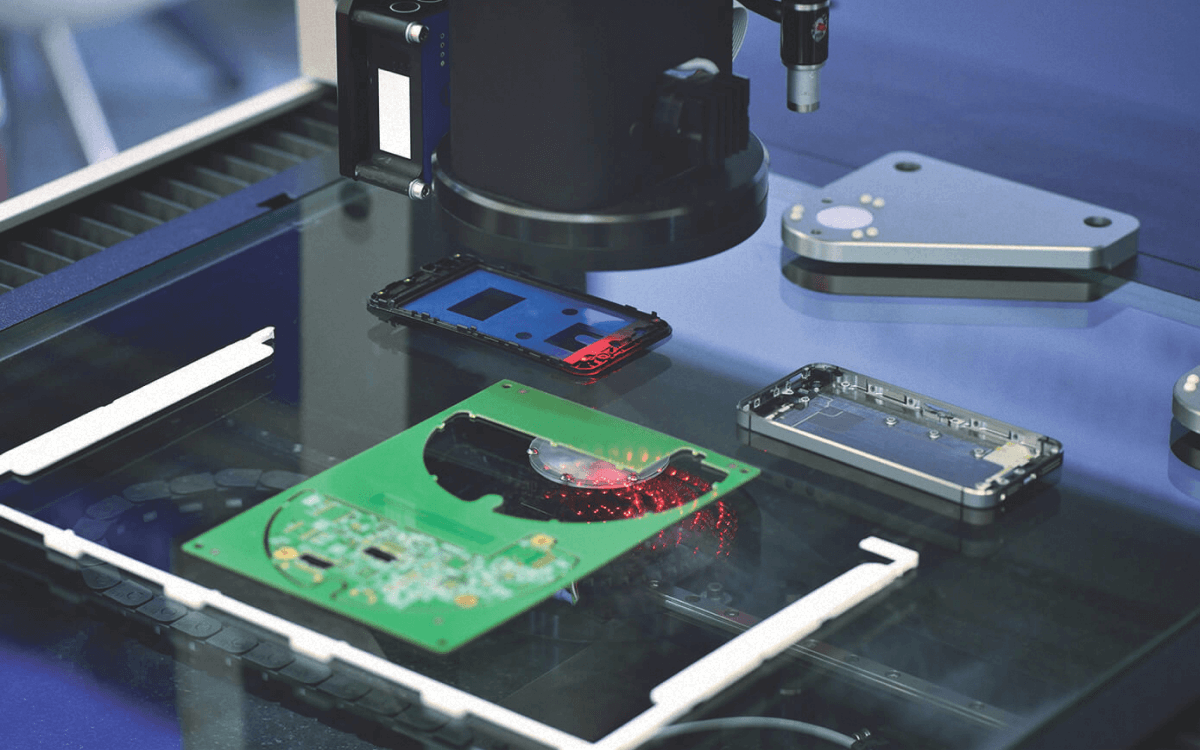
In manufacturing, current market volatility leads to immense operational pressures. Manufacturers need to respond quickly to decreased demand, disruption in the supply chain and interrupted retail channels. Leveraging AI to improve work efficiency is a great way to advance automation, control manufacturing processes distantly, and enable a remote workforce. And how is AI used in manufacturing? We’ll answer that question in the post, introducing computer vision applications in manufacturing and some real-life examples in production.
Outline
- Visual quality inspection
- Cost estimation
- Predictive maintenance
- Thermal imaging
- Wrapping up computer vision in manufacturing
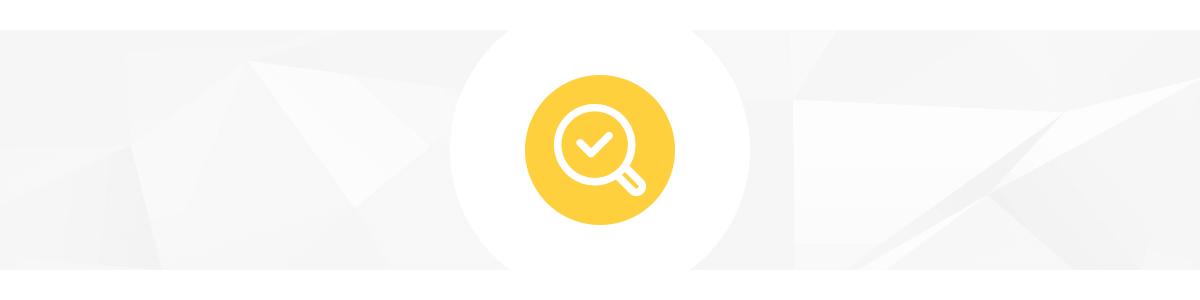
Visual quality inspection
Visual quality inspection is by far one the most popular and demanded computer vision use cases in manufacturing. There is no production line generating 100% indefectible and sound items. Traditional machinery inspection can cost millions of dollars and thousands of hours. Some flaws in production items can hardly be visible to the human eye as opposed to the computer vision-powered optical equipment that's able to detect even the smallest of defects. In recent years, machine vision manufacturing technologies have been helping manufacturers ease the inspection process and hence the operational pressures.
A great example of a company that implements such technology is AES, a Fortune 500 global power company, generating and distributing sustainable energy in 15 countries. The company owns eight wind farms with different capacities, starting from 500 up to 3000 wind turbines that need annual inspections. Initially, one check could take up to two weeks. Now, in partnership with Measure and Google's AutoML Vision, AES uses drones and automates the detection of defects, which allows them to prioritize maintenance of their high-value assets. Instead of climbing up the turbines with a large telephoto lens and then rappelling down to inspect the blade, drones now easily capture different angles, detect damages, and implement the whole inspection process in as fast as two days.
Another example is Bridgestone, a Japanese tire manufacturer, introducing a new car tire assembly system in 2016 called EXAMATION. It aimed to improve tire quality by providing real-time quality control in production based on 480 items – something that previously depended on human skills and judgment. As a result, Bridgestone claimed to achieve more than 15% improvement in uniformity compared to conventional manufacturing.
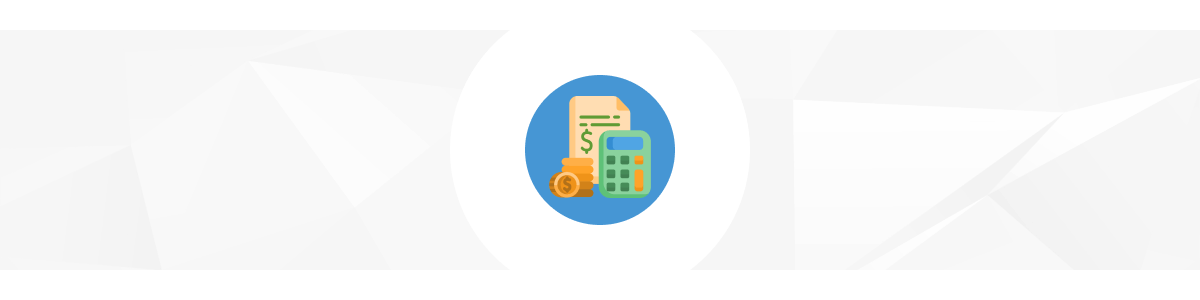
Cost estimation
An essential part of the manufacturing industry is machining. It's the process of cutting raw materials such as metal, wood, or plastic into a desired shape and size. Modern machine shops use computer-controlled precision machining tools for operations like cutting, drilling, boring, milling, etc. When a machine shop takes an order for building machinery parts, it needs to determine the individual cuts and holes that need to be made for each piece by carefully reading the blueprint provided by the customer. This manual process requires machining experts dedicated to the cost estimation process, which acts as a bottleneck for the productivity of the machine shop as a whole. Historically, a major challenge of the machining industry is the time-consuming task of cost estimation.
Computer vision can significantly simplify and accelerate the cost estimation task in machining. A well-trained AI model can analyze customers' blueprints and identify how many parts machine shops need to process, thus automatically calculating the cost within a fraction of a second. In Japan, a company named Kabuku has launched a similar solution with Google Cloud by handling the data management of their machine process. Kabuku aims to modernize the machining industry with 3D printing, cloud, and AI technologies for major manufacturing customers, including Toyota, Honda, and Olympus. The tool they use detects and highlights every object that requires machining processing. It then shows the detected types of processing steps, their quantity, cost, and the total estimated price for the entire item.
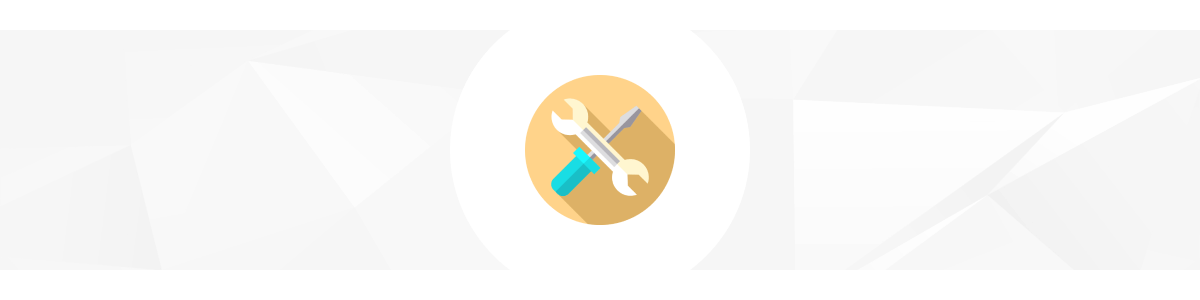
Predictive maintenance
As already discussed, conventional defect detection methods in manufacturing often result in resource waste and issues with product delivery. So it's no surprise that manufacturers seek to optimize resource utilization and predict failures before they happen. Predictive maintenance uses machine learning to learn from historical data and assess failure patterns using real-time data. It's all about reducing the downtime by either predicting failure, giving time to take corrective action, or decreasing the need for planned maintenance that's often stated in the manual.
To discover all potential applications of machine learning in manufacturing operations, Capgemini researched 300 manufacturers representing the top 75 global organizations in four manufacturing segments: automotive, consumer products, aerospace and defense, and industrial manufacturing. Here, they illustrate the predictive maintenance in action, by taking a look at how General Motors implements computer vision in manufacturing car pieces. They process images from robots mounted on assembly robots to spot signs and indications of failing mechanical components. The pilot test of this system detected 72 instances of failure across 7000 robots, identifying the problem before it could result in unplanned outages, and proving the effectiveness of predictive maintenance.
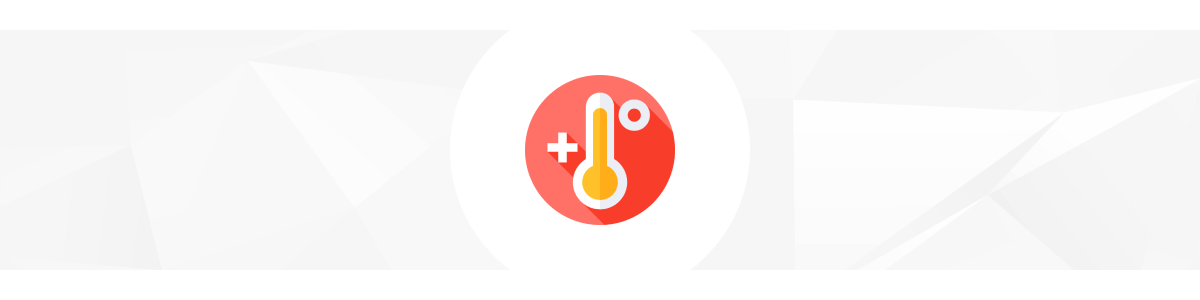
Thermal imaging
Thermal imaging, also known as infrared imaging, is another vision-powered preventative maintenance tool and an example of AI in manufacturing. Being used in bigger mechanical operations, thermal cameras detect overheated and overloaded components before they actually break down and cause facility downtime. They are also helpful for monitoring high-temperature industrial heaters, boilers, and furnaces.
Thermal imaging is especially useful in car manufacturing. Cars must be light to be fuel-efficient, but they must also be durable and strong. Modern car panels include a metal coating on top and a structural adhesive layer beneath to fulfill both of these aims. These layers are glued together using induction. However, this is a tricky process. For the adhesion to operate correctly, the temperature must be just right. The time it takes to accomplish this process depends on the type of glue used and the number of bonded joints needed; it usually takes about 40 to 45 seconds in total. Thermal cameras work perfectly to address this issue. When mounted correctly, they can follow the process and analyze the temperature changes, alerting if the temperature goes too high or too low. The technology can be designed to alert in case of an issue and trigger other actions, such as turning on a fan or taking other extra preventive measures.
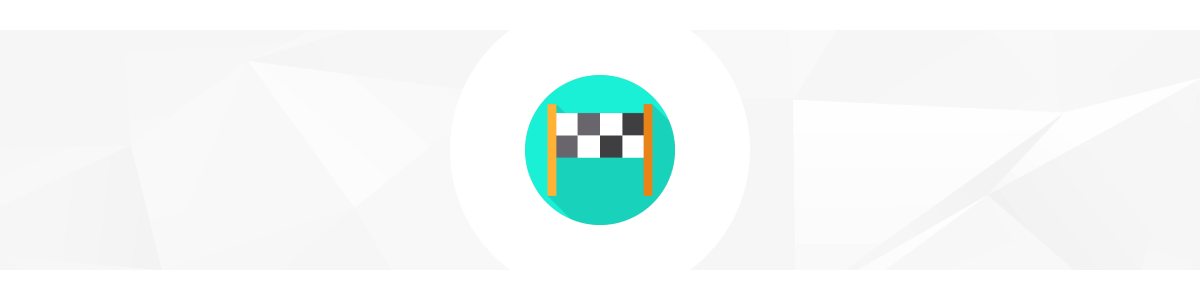
Wrapping up computer vision in manufacturing
As one of the most innovative and fast-evolving technologies, computer vision continuously enhances operational processes in various industries, such as healthcare, agriculture, autonomous driving, and, of course, manufacturing. Above, we discussed the most common applications of computer vision in the manufacturing industry, including visual quality inspection, cost estimation, predictive maintenance, and the use of thermal cameras, but who knows what the future of AI in manufacturing holds? Sure enough, more and more handy applications are invented and introduced every single day.
It's easy to praise computer vision and machine learning, but the technology itself is more complex. Businesses need some extent of maturity in data collection, management, and analytics to be able to extract the benefits of AI. Achieving considerable ROI with vision-powered AI projects demands time, purpose, and investment, especially when it comes to the manufacturing industry.
Clearly, the success of any computer vision project depends on the dataset quality used to train the AI model. Hence, to smoothly incorporate computer vision into your manufacturing tasks, the first step is defining and accurately labeling training data. That's something we're really good at, so in case you're seeking to build SuperData for your AI and scale your annotation processes, let us know.
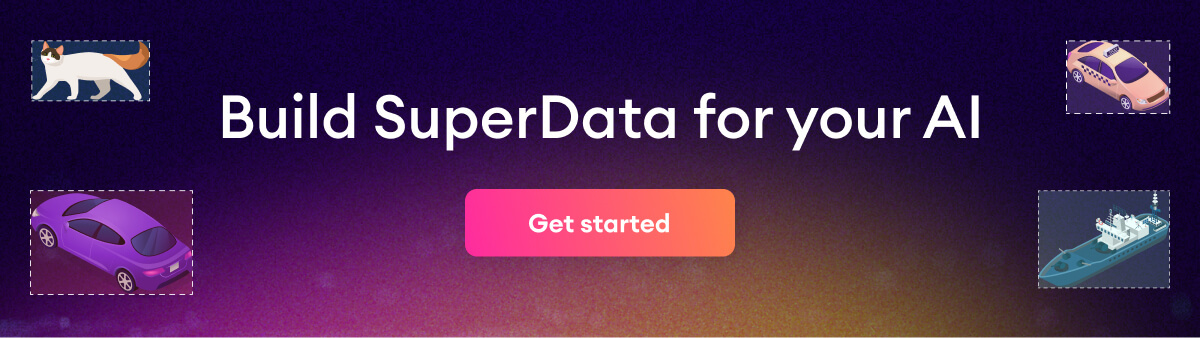